-
< Previous No article!
![]() |
||
![]() |
![]() ![]() ![]() |
![]() |
![]() ![]() |
Introduction to residual stress
|
Application field:
![]() |
![]() |
![]() |
![]() |
---|---|---|---|
![]() |
![]() |
![]() |
![]() |
Development of residual stress measurement techniques
- The residual stress testing methods are mainly divided into two categories: one is the mechanical release measurement method with certain damage, that is, the residual stress is released and measured by local failure of components, such as the stress release method and the blind hole method. Second, the method of physical measurement without damage, such as X-ray method, ultrasonic method, photoelastic method, magnetic measurement method. Magnetic measurement is a method to determine the magnitude and direction of residual stress through the change of magnetic permeability caused by ferromagnetic materials under the action of force. Magnetic measurement method has the advantages of portable instrument, simple operation, fast measurement speed and strong adaptability. Mastering and developing this technology is of great practical significance to industrial production and scientific research.
- In the 1960s, Japan, Germany, the former Soviet union and other countries carried out a lot of research on the residual stress of magnetic measurement method, and made abundant achievements. To this day, this method is still one of the most important methods for residual stress testing.
- The application of magnetic residual stress in China has never ceased. From the analysis of the residual stress of liquefied petroleum gas spherical tank, the research of the internal residual stress testing technology of plate components, the research of the residual stress of welding joints, the research of the residual stress of automobile spring steel plate, the research of the residual stress of ship welding to the stress testing system of high-speed railway wheels, the research of the residual stress of landing gear of fighter plane, etc.
The advantage of sex method in measuring residual stress:
- Completely non-destructive, no damage to the workpiece;
-
Rapid detection speed, easy to carry;
It can improve the frequency of sampling inspection, so as to ensure timely adjustment of the process and improve the stability of the product. - Simple operation, good reproducibility and reproducibility of detection results, and computer software storage results, easy to call at any time to see.
Three-dimensional residual stress testing system |
![]() |
---|
Test conditions:
- Suitable for steel, cast iron and other ferromagnetic materials
- No dirt, oil film and oxide layer on the surface
- No strong electromagnetic interference within 3m.
Parameters of the residual stress tester MRS-PLUS:
- Measuring frequency range: adjustable
- Single point test time is less than 2m
- The sensitivity: >10μA/MPa
- Repeated measurement error: ≤ ±25MPa
- Power supply:AC220±5%,50Hz±2%
- power≤100W
- Weight:5.00 Kg
- Sensor size:standardφ16mm(customizable)
Other features:
- Instruments can be used with automation equipment (optional)
- Easy to use and mobile to use
- Software can be customized according to customer requirements (optional)
- On-line inspection
![]() |
---|
![]() |
www.aittest.com |
Comparison of magnetic and X-ray applications:
portability | The depth of the test | Tester requirements | The test of time | zonation test technique | |
---|---|---|---|---|---|
Magnetic method | Convenient for outdoor testing | 0-5mmstress | General tester | Shorter | Can be lossless hierarchical testing |
X ray method | Difficulty in outdoor testing | Surface stress | Professional tester | Long | Must be lossy |
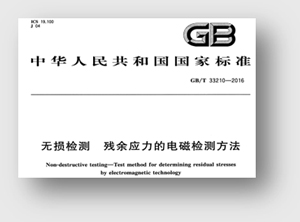
Typical customers
![]() |
![]() |
---|---|
![]() |
|
![]() |
![]() |
![]() |
![]() |
AITTEST®
-
As an international leading research and development center in the field of (MTT) technology, AITTEST focuses on:
Innovation of nondestructive testing technology
Deep research on magnetic technique
Development of automation and intelligent testing technology
Automation plant upgrade - Application-oriented solutions cover the entire value chain with the aim of strengthening the competitive position of industry partners at the domestic and international levels.
AITTEST provides users and research partners with a full range of non-destructive testing technologies, both in the field of basic research and applied research. Our researchers, engineers, and technicians work on the development of modern automated intelligent test applications, including feasibility studies, consulting, training and inspection services, and the creation of system prototypes.
Please contact the local authorized dealer:
- COMPANY:
- ATTEN:Mr. CHENG
- Mob:+86 13910088723
- TEL:
- FAX:
- E-MAIL:kingcyy@126.com
- ADD:
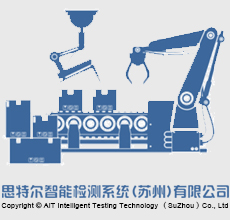